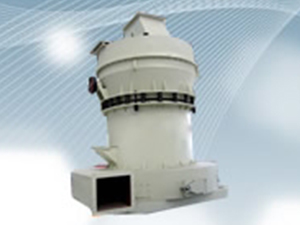
Three-ring medium-speed mill It is mainly suitable for non-flammable and explosive brittle materials with medium and low hardness and Mohs hardness ≤6, such as calcite, chalk, limestone, dolomite, kaolin, bentonite, talc, mica, Magnesite, illite, pyrophyllite, vermiculite, sepiolite, attapulgite, rectorite, diatomaceous earth, barite, gypsum, pigment, clay, alunite, graphite, fluorite, phosphate rock, There are hundreds of materials such as potash ore and pumice, and the fineness of the discharged product can be adjusted within the range of 325 mesh to 2500 mesh. New Raymond machine
table of Contents
1 Equipment use
2 Equipment characteristics
3 Equipment structure
4 working principle
Equipment usageedit
Three-ring medium-speed mill It is mainly suitable for non-flammable and explosive brittle materials with medium and low hardness, Mohs hardness ≤6, such as calcite, chalk, limestone, dolomite, kaolin, bentonite, talc, mica, Magnesite, illite, pyrophyllite, vermiculite, sepiolite, attapulgite, rectorite, diatomaceous earth, barite, gypsum, pigment, clay, alunite, graphite, fluorite, phosphate rock, There are hundreds of materials such as potash ore and pumice, and the fineness of the discharged product can be adjusted within the range of 325 mesh to 2500 mesh.
Equipment characteristicsedit
1. Low investment cost. Under the same fineness, it has less investment than jet mill, low cost and short recovery period;
2. Under the same finished product fineness and power consumption, the output is 45% higher than that of jet mill and stirring mill;
3. The wearing parts are low in loss, all wearing parts are made of high wear-resistant materials, and the service life is longer than the wearing parts of ordinary mill equipment;
4. The operation in the grinding cavity is safe and reliable, and the sealing performance is better compared with ordinary mills;
5. The finished product has high fineness, which can reach the range of 325-2500 mesh;
6. Environmental protection and pollution-free. The use of high-efficiency pulse dust collector, no dust pollution during the operation of the whole set of equipment, equipped with silencer and silencing room to reduce noise, production in accordance with national environmental protection standards, played an environmental role in the surrounding environment.
Working principleedit
The main motor of the three-ring micro-powder mill drives the main shaft and each layer of the turntable to rotate through the reducer, and the turntable drives dozens of ring rollers to roll and rotate in the grinding ring raceway through the pin. The bulk material is crushed into small particles by the hammer crusher and then sent to the storage bin by the elevator. The electromagnetic vibrating feeder sends the material evenly to the middle of the upper turntable. The material is scattered to the periphery of the circle under the action of centrifugal force. The raceway falling into the grinding ring is crushed by ring rolling, rolling, grinding, and crushing. After being crushed by one layer, the material falls into the second and third layers. The suction effect of the high-pressure centrifugal fan draws outside air into the machine. And the coarse powder after the third layer of pulverization is brought into the classifier. The vortex generated by the rotating turbine in the classifier causes the coarse particles to fall and regrind, and the fine powder enters the cyclone powder collector with the airflow and is discharged from the discharge valve at the bottom of the cyclone. The finished product is the airflow with a small amount of fine dust. After being purified by a pulse dust collector, it is discharged through a fan and a muffler.