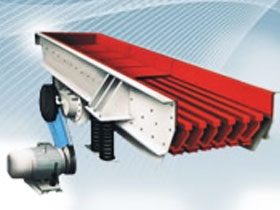
The vibrating screen works by using the reciprocating vibration generated by the vibrator. The upper rotating weight of the vibrator causes the screen surface to produce plane whirling vibration, while the lower rotating weight causes the screen surface to produce cone-shaped rotary vibration. The combined effect of the vibrator causes the screen surface to produce multi-rotating vibration. Its vibration trajectory is a complicated spatial curve. The curve is projected as a circle on the horizontal plane, and projected as an ellipse on the vertical plane. The amplitude can be changed by adjusting the excitation force of the upper and lower rotating weights. Adjusting the spatial phase angle of the upper and lower weights can change the curve shape of the screen surface movement trajectory and change the movement trajectory of the material on the screen surface. New Raymond machine
Chinese name vibrating screen Foreign name vibrating screen Advantages High efficiency, light weight, screening of dry materials Types of mine vibrating screen, fine vibrating screen, sieve shaft type reciprocating rotary vibration generated by the vibration of the original vibrator Science Department Ecological environment
table of Contents
1 Introduction
2 types
3 categories
▪ Linear vibrating screen
▪ Circular vibrating screen
▪ Oval sieve
▪ Thin oil vibrating screen
4 Operation check
5 Advantages of vibrating screen
6 Mechanical structure
▪ Vibrator
▪ Screen box
▪ Supporting device
▪ Transmission
7 working principle
8 work characteristics
9 Scope of application
10 Instructions for use
▪ Daily maintenance
▪ Regular maintenance
11 Standard Operating Procedure
12 Main function
▪ In engineering application
▪ Innovation of design theory and method
▪ Theoretical innovation of nonlinear dynamics
13 Weight adjustment
14 common faults
15 Maintenance plan
16 Application Needs
17 Skills
18 Industry Standards
19 Influencing factors
20 Classification
▪ Spiral flash vibrating screen
▪ Rotary vane vibrating screen
21 Practical application
22 Development Trend
23 Distribution of Manufacturers
24 Model building
25 Reasons for running pulp
26 Daily maintenance
27 Bearing damage prevention
Introduction editor
It is a filterable mechanical separation equipment used for solid phase treatment of mud, composed of a screen and a vibrator. The thickness of the screen is expressed by mesh, generally the size below 50 mesh is the coarse screen, and the size above 80 mesh is the fine screen. The vibrator is an eccentric wheel, which rotates under the drive of a motor to make the screen frame vibrate. Due to the vibration of the screen frame, the coarser solid particles remain on the screen surface when the slurry flows on the screen surface and are discharged from one end along the inclined plane. The finer solid particles and the slurry liquid flow together through the screen holes to the mud pool. .
Typeedit
The main types of vibrating screens: product advantages and disadvantages: high efficiency, light weight, complete and diverse series, multiple levels, and can meet the needs for dry material screening. For materials with high water content and adhesion, this model is not suitable. Vibration makes the materials more tightly adhere to the screen surface during operation, causing material congestion or forced shutdown. Due to the limitation of the working principle, this model consumes relatively high energy, especially under the conditions of high output. In addition, working noise and dust are heavy.
Classificationedit
Vibrating screening equipment can be divided into: mining vibrating screen, light fine vibrating screen, and experimental vibrating screen according to its weight.
Mine vibrating screens can be divided into: high-efficiency heavy-duty screens, self-centering vibrating screens, oval vibrating screens, dewatering screens, circular vibrating screens, banana screens, linear vibrating screens, etc.
Light-duty fine vibrating screen can be divided into: rotary vibrating screen, linear screen, straight row screen, ultrasonic vibrating screen, filter screen, etc. Refer to vibrating screen series
Experimental vibrating screen: flapping screen, top-strike vibrating screen, standard inspection screen, electric vibrating screen, etc. Please refer to the experimental equipment
According to the material running track of the vibrating screen, it can be divided into:
According to the linear motion track: linear vibrating screen (the material moves forward on the screen surface in a straight line)
According to the circular motion trajectory: the structure and advantages of the circular vibrating screen (the material moves in a circular motion on the screen surface)
According to the reciprocating motion track: fine screening machine (the material moves forward and backward on the screen)
Vibrating screens are mainly divided into linear vibrating screens, circular vibrating screens, and high-frequency vibrating screens. According to the type of vibrator, vibrating screen can be divided into single shaft vibrating screen and double shaft vibrating screen. The single-axis vibrating screen uses single unbalanced re-excited vibration to make the screen box vibrate, the screen surface is inclined, and the motion track of the screen box is generally circular or elliptical. The double-shaft vibrating screen is re-excited by double unbalanced synchronous counter-rotation, the screen surface is horizontal or gently inclined, and the motion track of the screen box is a straight line. Vibrating screens include inertial vibrating screens, eccentric vibrating screens, self-centering vibrating screens and electromagnetic vibrating screens.
Linear vibrating screen
Vibrating screen is a screening machine widely used in coal and other industries for material classification, washing, dewatering, and de-intermediation. Among them, the linear vibrating screen has been widely used due to its high production efficiency, good classification effect and convenient maintenance. In the working process, the dynamic performance of the vibrating screen directly affects the screening efficiency and service life. The vibrating screen uses a vibrating motor as the source of vibration, so that the material is thrown up on the screen while moving forward in a straight line. The material enters the inlet of the screening machine evenly from the feeder and produces several specifications through the multi-layer screen. The oversieve and undersieve are discharged from their respective outlets. The linear vibrating screen (linear screen) has the advantages of stability and reliability, low consumption, low noise, long life, stable vibration shape, and high screening efficiency. It is a new type of high-efficiency screening equipment, which is widely used in mining, coal, smelting, and building materials. , Refractory materials, light industry, chemical industry and other industries.
The circular vibrating screen (circular vibrating screen) is a new type of multi-layer, high-efficiency vibrating screen with circular motion. The circular vibrating screen adopts a cylindrical eccentric shaft exciter and an offset block to adjust the amplitude. The material sieving line is long, and the screening specifications are many. It has a reliable structure, strong excitation force, high screening efficiency, low vibration noise, sturdiness and durability. Convenient and safe to use, circular vibrating screens are widely used in product classification in mining, building materials, transportation, energy, chemical and other industries. According to material products and user requirements, high manganese steel woven screens, perforated screens and rubber screens can be used. There are two types of single-layer and double-layer screens. All kinds of screens can meet the different requirements of screening effects. This series of circular vibrating screens are seat-mounted. The inclination angle of the screen can be adjusted by changing the height of the spring support.
Oval sieve
The elliptical screen is a vibrating screen with an elliptical motion track, which has the advantages of high efficiency, high screening accuracy, and wide application range. Compared with the ordinary sieving machine of the same specification, it has larger processing capacity and higher screening efficiency. It is suitable for solvent and cold sintered ore screening in the metallurgical industry, ore classification in the mining industry, and grading, dehydration and de-intermediation in the coal industry. It is an ideal substitute for the existing large-scale vibrating screen and imported products from abroad. TES triaxial elliptical vibrating screen is widely used in quarry, sand and gravel screening operations, and can also be used for product classification in coal preparation, ore dressing, building materials, construction, power and chemical industries.
Screening principle: the power is transmitted from the motor to the active shaft of the vibration exciter and the gear vibrator (speed ratio is 1) from the motor through the V-belt. The three shafts rotate at the same speed to generate the exciting force. The vibration exciter and the screen box are connected by high-strength bolts , Produces elliptical motion. The material moves on the screen surface with the high-speed elliptical movement of the screen machine, rapidly stratifies, penetrates the screen, and moves forward, and finally completes the classification of the material.
Obvious advantages of TES series triaxial elliptical screen
The three-axis drive can make the screen machine produce an ideal elliptical motion. It has the advantages of a circular vibrating screen and a linear vibrating screen, and the elliptical trajectory and amplitude are adjustable. The vibration trajectory can be selected according to the actual material condition, and it is more difficult to screen materials. Have advantages
The three-axis drive is forced to synchronously excite, which can make the screen machine obtain a stable working state, which is especially advantageous for screening that requires a large amount of processing;
The three-axis drive improves the stress state of the screen frame, reduces the load of a single bearing, the side plate receives uniform force, reduces the stress concentration point, improves the stress condition of the screen frame, and improves the reliability and life of the screen machine. The large-scale machine has laid the theoretical foundation.
Due to its horizontal installation, the height of the unit is effectively reduced, which can well meet the needs of large and medium-sized mobile screening units.
The bearing is lubricated with dilute oil, which effectively reduces the bearing temperature and improves the life; the same screening area, the output of the elliptical vibrating screen can be increased by 1.3 to 2 times.
Thin oil vibrating screen
The thin oil vibrating screen has large processing capacity and high screening efficiency; the vibrator adopts bearing thin oil lubrication and an external block eccentric structure. It has the characteristics of large excitation force, low load, low temperature and low noise (the temperature rise of the bearing is less than 35°); the overall disassembly and assembly of the vibrator is convenient for maintenance and replacement, which greatly shortens the maintenance cycle (replacement of the vibrator only needs 1 to 2 Hours); the side plate of the screen adopts the whole plate cold work, no welding, high strength and long service life. The crossbeam and the side plate are connected by torsion shear high-strength bolts, no welding, and the crossbeam is easy to replace; the screen machine adopts rubber springs to reduce vibration, compared with metal springs, it has low noise, long life, stable cross-vibration zone, and each screen machine The fulcrum has the advantages of small dynamic load; the motor and the vibration exciter are connected by a flexible coupling, which has the advantages of long service life and small impact on the motor.
This screen machine series is widely used in the classification operation of coal, metallurgy, hydropower, mining, building materials, chemical industry, electric power, transportation, port and other industries.
Operation checkedit
The equipment needs to be assembled and tested without load before leaving the factory. It can be delivered after inspection of all indicators. Therefore, after the equipment is shipped to the site of use, the user should check the entire machine according to the packing list and the complete set of equipment delivery orders. Whether the parts are complete, and whether there are any omissions in the technical documentation.
After the equipment arrives at the site, it should not be placed directly on the ground. It should be placed steadily on flat sleepers, and the distance from the ground should not be less than 250mm. If stored in the open air, it should be covered with oil-proof cloth to prevent wind and rain erosion.
High-frequency vibrating screen is abbreviated as high-frequency screen. High-frequency vibrating screen (high-frequency screen) is composed of vibration exciter, slurry distributor, screen frame, frame, suspension spring and screen mesh.
The high frequency vibrating screen (high frequency screen) has high efficiency, small amplitude and high screening frequency. The principle of high-frequency vibrating screen is different from that of ordinary screening equipment. Because high-frequency vibrating screen (high-frequency screen) uses high frequency, on the one hand, it destroys the surface tension of the slurry and the high-speed oscillation of fine materials on the screen surface, accelerating The high density of useful minerals and the separation effect increase the probability that materials smaller than the separated particle size will contact the mesh.
Advantages of vibrating screen
It is mainly composed of screen box, vibration exciter, suspension (or support) device and electric motor.
The machine is driven by the V-belt to rotate the main shaft of the exciter. Due to the centrifugal inertia force of the unbalanced weight on the exciter, the screen box is vibrated. By changing the eccentric weight of the exciter, different amplitudes can be obtained.
The main advantages of vibrating screen:
1. Due to the strong vibration of the screen box, the phenomenon of material blocking the screen holes is reduced, so that the screen has a higher screening efficiency and productivity.
2. Simple structure, convenient to dismantle and replace the screen surface.
3. The power consumption for screening each ton of materials is small.
Mechanical structure
Vibrating screen is generally composed of vibrator, screen box, support or suspension device, transmission device and other parts.
Vibrator
There are generally two types of vibrators for single-shaft vibrating screen and double-shaft vibrating screen according to the eccentric reconfiguration modeType. The block eccentric type is better for eccentric weight configuration.
Screen box
The screen box is composed of a screen frame, a screen surface and a pressing device. The screen frame is composed of side plates and beams. The screen frame must be sufficiently rigid.
Support device
The supporting device of the vibrating screen has two types: hanging type and seat type. The seat type installation is relatively simple, and the installation height is low, generally should be preferred. The supporting device of the vibrating screen is mainly composed of elastic elements, commonly used coil springs, plate springs and rubber springs.
transmission
The vibrating screen usually adopts a V-belt transmission device. The structure of the vibrating screen is simple, and the number of revolutions of the vibrator can be selected arbitrarily, but the belt is easy to slip during operation, which may cause the screen hole to block. Vibrating screens are also directly driven by couplings. The coupling can maintain a stable number of revolutions of the vibrator and has a long service life, but it is difficult to adjust the number of revolutions of the vibrator.
Working principleedit
The process of dividing the scattered material groups with different particle sizes through a single-layer or multi-layer sieve surface with uniformly-distributed holes multiple times and dividing them into several different levels is called screening. The particles larger than the sieve opening remain on the screen surface and are called the oversieve of the sieve surface. The particles smaller than the sieve opening pass through the sieve opening and are called the undersieve of the sieve surface. The actual screening process is: after a large number of broken materials with different particle sizes and mixed thicknesses enter the screen surface, only a part of the particles are in contact with the screen surface. Due to the vibration of the screen box, the material layer on the screen is loosened, so that large particles exist. The gap is further enlarged, and small particles take the opportunity to pass through the gap and transfer to the lower layer or transporter. Because the gap between small particles is small and large particles cannot pass through, the original disorderly arrangement of particle groups separates, that is, they are stratified according to particle size, forming an arrangement rule with small particles on the bottom and coarse particles on the top. The fine particles that reach the sieve surface, the ones smaller than the sieve hole, can pass through the sieve, and finally the coarse and fine particles are separated and the screening process is completed. However, there is no sufficient separation. During sieving, there is generally a part of the undersize material remaining on the oversize material. When fine particles pass through the sieve, although the particles are smaller than the sieve hole, they have different degrees of difficulty. The material and the particles with the same sieve hole size are more difficult to penetrate the sieve, and it is even more difficult to penetrate the gap between the particles under the sieve surface.
Work characteristicsedit
① Adopt block eccentricity as the exciting force, which is strong.
② The screen beam and screen box adopt high-strength bolts, with simple structure and convenient and quick maintenance;
③Using tire coupling, flexible connection, stable operation;
④. The structure of small amplitude, high frequency and large inclination angle makes the machine high in screening efficiency, large in processing, long in life, low in power consumption and low in noise.
According to the structure and working principle of the screening machine, there are roughly the following categories:
1. The working surface of the roller screen is composed of a horizontally arranged rolling shaft.
2. Roller screen The working surface is composed of rolling shafts arranged horizontally. The working part of the fixed screen is fixed, and the material is screened by sliding along the working surface. Fixed grid sieve is one of the most widely used in concentrators, generally used for pre-screening before coarse or medium crushing. It has a simple structure and is convenient to manufacture. It does not consume power and can directly unload the ore onto the screen surface. The main disadvantages are low productivity and low screening efficiency, generally only 50-60%.
3. Plane motion screen The body is swinging or vibrating in a plane. According to its plane motion trajectory, it is divided into linear motion, circular motion, elliptical motion and complex motion. Shaking screens and vibrating screens fall into this category.
Scope of applicationedit
The scope of application of vibrating screens is very wide, and almost all aspects of life need to use various types of vibrating screens in processing and manufacturing.
Vibrating screens are mainly used in mining, coal, smelting, building materials, refractory materials, light industry, chemicals, medicine, food and other industries.
Vibrating screens are the most widely used in concentrators. According to their different transmission mechanisms, they can be divided into the following types: eccentric vibrating screen, inertial vibrating screen, self-centering vibrating screen, resonance screen.
Instructions for useedit
1. Screening machine design,Exquisite and easy to assemble, one person can operate the screen machine.
2. Compared with other types of screening equipment, it has a larger screening area and high-efficiency processing capacity.
3. Unique screen structure design, convenient and quick to replace the screen (only 3 to 5 minutes), in addition, this design allows the use of various screens (nylon, special dragon, PP mesh).
4. The mother net completely supports the fine mesh, so the fine mesh can have a longer lifespan, and the use of fine mesh consumables is reduced. The long-term production process can reduce many costs.
Function and principle:
The basic principle is to use the weights (unbalanced weights) installed at the upper and lower ends of the motor shaft to convert the rotation of the motor into a horizontal, vertical, and inclined three-dimensional motion, and then transmit this motion to the screen surface. Changing the phase angle of the upper and lower weights can change the direction of travel of the raw materials.
Daily maintenance
Before starting:
1. Check whether the coarse and fine meshes are damaged
2. Whether each group of tie rings are locked
3. Check whether the V-shaped ring of the screen frame of the rotary vibrating screen is damaged. If there is damage, it needs to be repaired in time to prevent material leakage.
2. At startup:
1. Pay attention to whether there is abnormal noise and whether the current is stable
2. Whether the vibration is abnormal
3. After use: clean up after each use.
Regular maintenance
Regularly check the coarse mesh, fine mesh and spring for fatigue and damage, and whether various parts of the fuselage are damaged due to vibration. The parts that need to be lubricated must be lubricated. Vibration: With models, screen surface specifications, screen surface layers, screen hole size, feed particle size, processing capacity, motor power, vibration frequency, double amplitude data, these data can give people searching for vibrating screens a deeper understanding.
Standard operating proceduresedit
Check before running the vibrating screen: including equipment sanitation, complete, fastened, and intact bolts at all parts, check whether the exciter is intact, check whether the springs are damaged, missing, or broken, and check whether the V-belt is tensioned or broken Whether the sieve box and sieve plate are damaged, check whether the sieve plate is blocked by debris, and the screen surface should be flat without damage or looseness, check whether the inlet and outlet chute is unblocked, check whether the beam has open welding, etc., and check whether the safety protection device is safe and reliable. Check whether the control box, communication and lighting are intact, whether the grounding protection is reliable, and whether the control buttons are flexible and reliable.
When starting: After turning on the vibrating screen, stand by the control box and monitor the equipment to start and stop immediately if abnormalities are found. After the start-up is normal, check whether the nozzle of each vibrating screen is blocked or falling off. Always observe the temperature and sound of the motor, often observe the sound of the exciter, and observe whether the vibration of the sieve is consistent with the four corners and whether the triangle belt is leaking. Loose or fall off, often observe the effect of dehydration and release. Check whether the sieve inlet and outlet are normal or not blocked.
Stop: Stop the machine after the material on the sieve is exhausted. When parking, observe whether the sieve collides with other equipment when passing through the resonance point. When the following situations are found, it must be stopped immediately. When encountering personal safety or equipment safety, when there are too many debris on the screen area and the unloading is not smooth, the screen is broken in a large area, the chute under the screen is seriously blocked, the screen box is severely swinging and other abnormal conditions. After the problem is eliminated, the vibrating screen can be restarted.
Main roleedit
With the further development of China's economic construction and scientific research, new-purpose vibrating screens will continue to appear, and their use in various departments will also increase, and they will play an increasingly important role.
In engineering application
In the past 30 years, Professor Wen Bangchun has promoted the theoretical and application results obtained in engineering practice. For example, large-scale vibration exciter deflection type self-synchronizing vibrating screen, inertial resonance probability screen, new structure vibrating crusher, new structure vibrating cooler, etc., have been successfully applied in the industrial sector, and have achieved significant economic and social benefits , Won more than 10 national invention awards, national science and technology progress awards and provincial and ministerial awards.
Innovation of design theory and method
A more systematic dynamic design theory and method of vibrating screen machinery is proposed, especially the dynamic design theory and method of nonlinear vibrating screen nanomachine, and the comprehensive design method with dynamic optimization, intelligent optimization and visual optimization as the content, which is high-quality The design of such products, especially the research and development of new products, provides theoretical references and basis for the factory.
Nonlinear dynamics theory innovation
Summarizing Professor Wen Bangchun’s long-term systematic research and experimentation on vibration and wave utilization technology and equipment working theory, it is used for vibrating screens using multiple branches of engineering (such as the application of vibration synchronization and control synchronization theory, nonlinear vibration Branches such as utilization, the utilization of ripple energy, etc.) have created the theoretical basis.
Hammer adjustmentedit
Because part of the work of the vibrating screen is delicate operation, it is impossible to avoid such problems during operation. Sometimes when the material is screened, the discharge situation is different. At this time, the material screening can be adjusted by adjusting the upper and lower weights. To achieve better results.
First of all, we can adjust the additional weight of the vibrating motor. There are additional weights on one side of the upper and lower weights (upper and lower eccentric blocks), which can increase the vibrating force of the vibrating screen, according to the specific gravity and selection of the material to be screened by the customer Depending on the number of layers of the vibrating screen, appropriately increase or decrease the excitation force and adjust the number of additional weights. Secondly, the phase angle of the upper and lower weights of the vibrating motor can be changed, which changes the residence time and movement trajectory of the material on the vibrating screen.
Furthermore, the bottom cylinder of the vibrating screen can be opened, the fixing bolts of the lower weight can be loosened, and the phase angle of the upper and lower weights can be adjusted in the opposite direction to the discharge port of the vibrating screen according to the movement track of the material screened by the vibrating screen. Then put some materials on the vibrating screen, let the vibrating screen energize and run, and observe the movement trajectory of the materials on the screen. If the separation efficiency of the material, the screening rate, the processing capacity, and the distribution of the material on the screen surface are relatively even, you can stop the machine and tighten the fixing bolts.
Common faultsedit
1. The motor rotates poorly
2. Abnormal sound
3. Raw materials cannot be discharged automatically
4. The fine net is easy to break
5. The outlet of the discharge frame is cracked
Daily maintenance:
1. Before starting: check whether the coarse and fine meshes are damaged, and whether each group of tie rings is tightly locked
2. When starting: pay attention to whether there is abnormal noise, whether the power supply is stable, and whether there is abnormal vibration
3. After use: clean up after each use, regular maintenance:
(1) Regularly check whether the coarse and fine meshes and springs are fatigued and damaged, and whether various parts of the fuselage are damaged due to vibration.
(2) When the motor runs for two weeks, it must be replenished with timely lithium grease (ZL-3). Accumulatively run for l500 hours, check the bearing and replace it immediately if it is damaged.
Maintenance planedit
Polymer materials control really screen wear
During the operation of the vibrating screen, parts are often worn and scratched due to the "hard-to-hard" metal fitting relationship, such as the wear of the main shaft bearing of the vibrating screen. After the above problems, the company’s traditional solution is repair welding or machining repair after brush plating, but both have certain drawbacks: the thermal stress generated by the high temperature of repair welding cannot be completely eliminated, and there is neither the effect of repair welding thermal stress nor the repair thickness. Restricted, and at the same time, the product has a retreat that the metal material does not have. It can absorb the shock and vibration of the equipment, avoid the possibility of re-wearing, and greatly extend the service life of the equipment components, saving a lot of downtime for the company and creating a huge economy value.
Application notesedit
The pharmaceutical industry and people’s bodies are closely related. Therefore, the country has very strict requirements on the pharmaceutical industry. The pharmaceutical industry also requires very strict material screening. The most basic thing is that the vibrating screening equipment used in the pharmaceutical industry must be stainless steel 304 or even 316 material, no impurities are allowed in the contact material part, so the rubber accessories must also meet the food-grade hygiene standards (silica gel), and the screening equipment required by the pharmaceutical industry must pass the GMP production standard. The use of vibrating screens in pharmaceuticals has very strict requirements and must meet the GMP production standards of the pharmaceutical industry. This relates to whether the drugs that pass the screening will be contaminated.
In fact, as an uncomplicated screening machine, the so-called GMP standard actually means that the material must be 304 stainless steel. In the selection of rubber parts, the pharmaceutical grade must be selected. The equipment must be polished internally and externally without black spots. , No glitches.