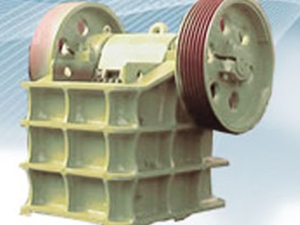
Jaw crusher is commonly known as jaw crusher, also known as tiger mouth. The crushing chamber is composed of two jaw plates, a movable jaw and a static jaw, which simulates the movement of the animal's jaws to complete the material crushing operation. It is widely used in the crushing of various ores and bulk materials in mining and smelting, building materials, highways, railways, water conservancy and chemical industries. The high compressive strength of the crushed material is 320Mpa. Raymond machine price
Chinese name Jaw Crusher Foreign name Jaw Crusher Other name Jaw Crusher Performance The most commonly used ore crusher Advantages High efficiency Classification Single pendulum jaw type, compound pendulum jaw type
1 Development Overview
2 Introduction
3 categories
▪ Single pendulum jaw principle
▪ Principle of compound pendulum jaw
4 advantages
5 Operation steps
6 Maintenance
7 matters needing attention
8 Troubleshooting
9 Safe operation
10 Troubleshooting
11 Design and material selection
12 Assembly
13 Influencing factors
14 Periodic inspection
15 Maintenance method
Development overviewedit
Modern crushing machinery was created after the gradual improvement and promotion of power machinery such as steam engines and electric motors.
In 1806, a roller crusher driven by a steam engine appeared;
In 1858, Black in the United States invented the jaw crusher to crush rocks;
In 1878, the United States developed a gyratory crusher with continuous crushing action, and its production efficiency was higher than that of a jaw crusher with intermittent crushing action;
In 1895, William of the United States invented an impact crusher with lower energy consumption.
In the 1980s, the feed size of a large jaw crusher that crushed 800 tons of materials per hour had reached about 1800 mm.
Commonly used jaw crushers have two toggles and single toggles. The former only makes a simple circular arc swing when working, so it is also called a simple swing jaw crusher; the latter moves up and down while making circular arc swing.
Jaw Crusher
Jaw Crusher
The technical level of domestic jaw crusher manufacturers is very different. There are a few manufacturers whose products are basically close to the world's advanced level, while most of the manufacturers' products are far behind the world's advanced level. The jaw crusher frame accounts for a large proportion of the total machine quality (casting frame accounts for 50%, welding frame accounts for 30%). Foreign jaw crushers are all welded frames, and even movable jaws are also welded. Jaw crusher adopts welding frame is the development direction. There are many examples of unreasonable domestic jaw crusher frame structure design, the reason is that the reinforcement ribs are not arranged according to the actual force of the crusher
In recent years, with the increase in the proportion of open pit mining and the adoption of large electric shovels (excavators) and large mining vehicles, the size of the ore transported from open pit mines to the crushing workshop has reached 1.5 to 2.0 meters; at the same time, due to the original The grade of ore is decreasing day by day. If you want to maintain the original production capacity of the concentrator, you must greatly increase the amount of raw ore mined and crushed. Therefore, the jaw crusher is developing in the direction of large-scale. At present, the large-size jaw crusher manufactured abroad is: 3000×2100 mm (simple pendulum), ore lump size is 1800 mm, production capacity is 1100 tons/unit·hour; 2100×1670 mm (compound pendulum), When the discharge port is 355 mm, its production capacity is 3000 tons/unit·hour.
With the emergence of impact-resistant large rolling bearings, there is a trend to use compound pendulum jaw crushers instead of simple pendulum crushers at home and abroad. This is because under the same conditions, the production capacity of the former is increased by 30% compared with the latter; When the production capacity of the former is the same, the weight of the former is 20%~30% less than the latter. However, there are still some problems in the structure of the compound pendulum jaw crusher, which need to be studied and improved.
It should be noted that in recent years, due to the improvement of my country's large-scale rolling bearing materials and the needs of underground coarse crushing equipment, the compound pendulum jaw crusher has also developed to a large-scale direction. At present, the 900×1200 compound pendulum crusher is being trial-produced. With the enlargement of equipment specifications, the adjustment device and safety device of general jaw crushers must adopt new mechanisms. Therefore, another trend in the current development of jaw crushers is that the size of the discharge port adopts a hydraulic adjustment mechanism, which is not only simple and fast, and can be adjusted as needed at any time during work; at the same time, the overload safety device of the machine is also hydraulic Mechanism to achieve safety and reliability without damaging the thrust plate, and after troubleshooting, the machine immediately resumes work. Both at home and abroad are vigorously developing this hydraulic jaw crusher. my country has produced 900×1200 hydraulic simple pendulum jaw crushers and put them into production in Laiwu Iron Mine and Roots Iron Mine. Production practice has proved that the insurance mechanism and adjustment mechanism of the hydraulic jaw crusher have achieved the purpose of safety insurance and convenient adjustment. They are in good condition and are well received by post workers.
In terms of improving the crushing efficiency of the jaw crusher, in addition to making partial improvements to the original equipment structure, such as increasing the height of the crushing chamber to increase the production capacity; reducing the discharge port and increasing the crushing ratio; increasing the swing speed of the movable jaw, In addition to increasing equipment production capacity and improving product quality, various countries are currently researching and testing crushers with new structures, such as impact jaw crushers, double-action jaw crushers, and hydraulic drive jaw crushers. [1]
Introduction editor
Jaw crushers are mainly used as coarse crushers and medium crushers in mining, building materials, infrastructure and other sectors. According to the width of the feed port, it is divided into three types: large, medium and small. The width of the feed port is greater than 600MM for large machines, the width of the feed port is 300-600MM for medium-sized machines, and the width of the feed port is less than 300MM for small machines. machine. The jaw crusher has simple structure, easy manufacture and reliable operation.
The working part of the jaw crusher is two jaws, one is a fixed jaw (fixed jaw), which is vertically (or slightly inclined at the upper end) fixed on the front wall of the machine body, and the other is a movable jaw (moving jaw). Inclined to form a crushing cavity (working cavity) with a large upper and a lower jaw with the fixed jaw. The movable jaw plate makes periodic reciprocating motion against the fixed jaw plate, sometimes separating and sometimes approaching. When separated, the material enters the crushing cavity, and the finished product is discharged from the lower part; when it is close, the material installed between the two jaws is crushed by squeezing, bending and splitting.
Jaw crushers can be divided into simple swing jaw crushers (simple pendulum jaw crushers) according to the different swing modes of the movable jaw. There are three types of complex swing type jaw crusher (compound swing type jaw crusher) and comprehensive swing type jaw crusher.
Classificationedit
As far as jaw crushers are concerned, although the structure types are different, their working principles are basically similar, except that the movement trajectory of the moving jaw is different. In a nutshell, when the movable jaw plate cyclically reciprocates to the fixed jaw plate around the suspension axis, and sometimes approaches and leaves, when the movable jaw plate approaches the fixed jaw plate, the ore between the two jaw plates , Crushed by the combined action of crushing, splitting and bending; when the movable jaw leaves the fixed jaw, the crushed ore is discharged through the discharge port of the crusher under the action of gravity.
Single pendulum jaw principle
The movable jaw is hung on the mandrel and can swing left and right. When the eccentric shaft rotates, the connecting rod reciprocates up and down, driving the two thrust plates to also reciprocate, thereby pushing the movable jaw to reciprocate left and right to realize crushing and unloading. This type of crusher adopts a crank double-link mechanism. Although the movable jaw is subjected to a great crushing reaction force, its eccentric shaft and connecting rod are not subjected to much force. Therefore, large-scale and medium-sized machines are often used in the industry. To crush hard materials. In addition, when this type of crusher works, the motion trajectory of each point on the movable jaw is an arc centered on the mandrel, the arc radius is equal to the distance from the point to the axis, the upper arc is small, and the lower arc is large. The crushing efficiency is low, and the crushing ratio is generally 3-6. Because of its simple motion track, it is called simple swing jaw crusher.
The structure of the simple pendulum jaw crusher is compact and simple, and the eccentric shaft and other transmission parts are less stressed; due to the small vertical displacement of the movable jaw, there is less excessive crushing of materials during processing, and the wear of the movable jaw plate is less. [2]
Principle of compound pendulum jaw
The upper end of the movable jaw is directly suspended on the eccentric shaft as a crank connecting rod mechanism
Jaw crusher working simulation diagram
Jaw crusher working simulation diagram
The connecting rod is directly driven by the eccentricity of the eccentric shaft, and the lower end of the movable jaw is hinged and supported on the rear wall of the frame with the thrust plate. When the eccentric shaft rotates, the trajectory of each point on the movable jaw is from the circumferential line of the suspension point (the radius is equal to the eccentricity), gradually turning downwards into an ellipse, and the downward, the more the ellipse is, until the lower part and the thrust plate The locus of the connection point is a circular arc line. Because the movement trajectory of each point on the movable jaw of this machine is relatively complicated, it is called a complex swing type jaw crusher.
Compared with the simple pendulum jaw crusher, the advantages of the compound pendulum jaw crusher are: lighter weight, fewer components, more compact structure, better filling degree in the crushing cavity, uniform crushing of the loaded material, and moving the lower end of the jaw The finished product unloading is mandatory, so the productivity is higher, which is 20-30% higher than the productivity of the simple pendulum jaw crusher of the same specification; the material block has a large up and down movement under the movable jaw, which is easy to assume a cube shape Unload
Structure diagram
The jaw crusher is mainly composed of: fixed jaw plate, movable jaw plate, frame, upper and lower guard plates,
It is composed of adjusting seat and moving jaw rod. A good understanding of the internal structure of the jaw crusher can play a very helpful role in the use of the jaw crusher and when there are problems.
Crushing ratio
The crushing ratio is an important evaluation index for measuring the jaw crusher. The crushing ratio of the jaw crusher is the ratio of the raw material size to the accuracy of the crushed product. It indicates the degree of reduction of raw materials after crushing. After the ore is crushed, the particle size becomes smaller. The ratio of the particle size before the ore crushing to the particle size after the crushing is called the crushing ratio. It represents the multiple of the size reduction of the ore after crushing. There are several calculation methods for crushing ratio:
1. Use the large particle size before crushing and the large particle size after crushing to calculate the large particle size method. Our country often uses this calculation method in the design of the concentrator, because the design needs to determine the jaw crusher feed port according to the feed size width
2. Use the ratio of the effective width of the feed opening and the width of the discharge opening of the jaw crusher
For some jaw crushers, the discharge granularity is not determined by the size of the discharge opening.
3. Calculate with the average particle size before and after ore crushing, also called average crushing ratio
Features
1. Low noise and less dust.
2. The crushing ratio is large and the product size is uniform.
3. Simple structure, reliable work and low operating cost.
4. The lubrication system is safe and reliable, the replacement of parts is convenient, and the equipment maintenance is simple.
5. The crushing cavity is deep and there is no dead zone, which improves the feeding capacity and output.
6. Equipment energy saving: single machine energy saving 15%-30%, system energy saving more than doubled.
7. The adjustment range of the discharge opening is large, which can meet the requirements of different users.
working principle
When the jaw crusher is working, the movable jaw plate periodically reciprocates against the fixed jaw plate, sometimes approaching and sometimes leaving. When approaching, the materials are crushed by squeezing, splitting, and impact between the two jaws; when leaving, the crushed materials are discharged from the discharge port by gravity.
In the process of crushing huge rocks into small rocks, a crusher is usually the "main" crusher. The longest and most robust crusher is the jaw crusher. When feeding the jaw crusher, the material is poured into the crushing chamber containing jaw teeth from the top entrance, and the jaw teeth push the material against the chamber wall with huge force, breaking it into smaller stones. Supporting the movement of the jaw teeth is an eccentric shaft, which penetrates the body frame. Eccentric motion is usually produced by flywheels fixed at both ends of the shaft. Spherical roller bearings are often used for flywheel and eccentric support bearings. The bearings must withstand huge impact loads, abrasive sewage and high temperatures.